Повышение эффективности оборотных систем водопользования c использованием реагентов
Производство лакокрасочных материалов (ЛКМ) и сфера их применения является одним из крупных источников загрязнения окружающей среды: 5–10% общего количества промышленных загрязнений приходится на лакокрасочную промышленность.
Повышение эффективности оборотных систем водопользования c использованием реагентов
Производство лакокрасочных материалов (ЛКМ) и сфера их применения является одним из крупных источников загрязнения окружающей среды: 5–10% общего количества промышленных загрязнений приходится на лакокрасочную промышленность.
Количество сточных вод производства лакокрасочных материалов, виды и концентрация загрязняющих воду веществ колеблются в широких пределах и зависят от изготовляемого продукта и метода его получения. Состав загрязняющих веществ многокомпонентный. Отходы производства, предоставленные для анализа, представляют собой остатки сырья, материалов или полуфабрикатов, образовавшихся при изготовлении продукции, а также продукты физико-химической или механической переработки сырья.
При производстве лакокрасочных материалов сточные воды образуются при мойке основного и вспомогательного оборудования.
Сточные воды содержат различные взвешенные и водорастворимые вещества.
Качественный состав стоков непостоянен не только для одноименных производств различных заводов, но и для отдельно взятого производства во времени.
Взвешенные вещества представляют собой высокодисперсную часть пигментов с размерами частиц 1–15 мкм. Ориентировочная скорость их осаждения не более 0,05–0,2 мм/с. Уточненные расчеты осаждения рекомендуется проводить на основании экспериментальных данных.
В практике очистки подобных сточных вод применяется оборудование и сооружения различного типа [1–2].
Очистка сточных вод от взвешенных веществ осуществляется в отстойниках (ловушках) или на фильтр-прессах (после проведения контрольного фильтрования). В малотоннажных производствах очистка от взвешенных веществ может быть осуществлена в осадительных центрифугах и центробежных тарельчатых сепараторах. Отстойники, центрифуги и сепараторы подбирают путем расчетов и моделирования на основании экспериментальных данных.
Для интенсификации процесса осаждения взвешенных веществ в ряде случаев целесообразно использовать коагулянты, флокулянты, а также электрокоагуляцию. Уловленные пигменты или полупродукты возвращаются на соответствующие стадии технологического процесса. Очищенные сточные воды, как правило, могут быть использованы в системах оборотного водоснабжения.
Методика проведения испытаний заключалась в обработке проб сточных вод реагентами, дальнейшим осветлением воды путем отстаивания или флотации.
В качестве реагентов использовались следующие вещества:
- щелочь, 0,5–5%-ный раствор;
- коагулянт, 1–10%-ный раствор;
- флокулянт, 0,05%-ный раствор.
![]() |
Рисунок 1. Стадии реагентной обработки |
Порядок выполнения эксперимента
1. Приготовление растворов реагентов.
2. В цилиндры объемом 250 мл заливаются пробы сточных вод в количестве 150 мл в каждый.
В каждый цилиндр добавляются: раствор щелочи, раствор коагулянта с последующим перемешиванием, пауза 2–3 мин., в течение которых происходит интенсивное образование хлопьев.
Добавляется раствор флокулянта с последующим перемешиванием, что приводит к укрупнению хлопьев.
Экспериментальные дозировки реагентов приведены в табл. 1.
Таблица 1 Поисковые исследования определения оптимальной дозы реагентов |
|||||||||||||||||||||||||||||||||||||||||||||||||||||||||||||||||||||||||||||||||||||||||||||||||||||||||
|
Полученные смеси отстаивались 30 мин.
В чистый цилиндр наливали 100 мл воды, очищенной после I стадии, и добавляли раствор коагулянта и раствор флокулянта с последующим перемешиванием. Для интенсификации процесса коагуляции и флокуляции добавлялся осадок, образовавшийся в ходе I стадии.
Далее осуществляли отстаивание в течение 10–15 мин. и после этого фильтрование воды после II стадии через обеззоленный фильтр.
Затем проводили анализ отфильтрованной пробы на турбидиметре HACH 2100 для определения мутности пробы в единицах NTU.
В табл. 1 представлены данные поиска оптимальной дозы реагентов. В частности, при расходе 16 мл 0,5%-ного раствора щелочи, 0,9 мл 10%-ного раствора коагулянта и 1,6 мл 0,05%-ного раствора флокулянта получено минимальное значение мутности – 4,95 мг/л.
Полученные данные о качестве вод удовлетворяют требованиям к качеству воды, используемой в оборотном цикле.
Оптимальные дозы реагентов приведены в табл. 2.
Таблица 2 Оптимальные дозы реагентов, добавляемых в сточные воды |
||||||||||||||
|
Приготовление и дозирование реагентов осуществлялось в следующем режиме:
- концентрация маточного раствора щелочи – 10% масс. (100 г/л);
- концентрация рабочего раствора щелочи – 5% масс. (50 г/л);
- доза рабочего раствора щелочи – 5 л на 1 м3 стоков;
- концентрация маточного раствора коагулянта – 20% масс. (200г/л);
- концентрация рабочего раствора коагулянта – 10% масс. (100 г/л);
- доза рабочего раствора коагулянта – 2 л на 1 м3 стоков;
- концентрация маточного раствора флокулянта 655–0,1% (1 г/л);
- концентрация рабочего раствора флокулянта 655–0,05% (0,5 г/л);
- доза рабочего раствора флокулянта – 2 л на 1 м3 стоков.
На основе полученных экспериментальных данных была разработана принципиальная схема очистки сточных вод лакокрасочного производства (рис. 2).
![]() |
Рисунок 2 (подробнее)
Принципиальная схема очистки сточных вод |
На первой стадии в исходную сточную воду поочередно добавляются щелочь (реагент 1), коагулянт (реагент 2) и флокулянт (реагент 3), что при последующем перемешивании приводит к коагуляции взвешенных частиц. После введения коагулянтов наблюдалось активное образование хлопьев и их быстрое выпадение в осадок.
Далее, чтобы увеличить эффективность процесса очистки, применяются полимерные флокулянты. Благодаря своей очень большой молекулярной массе эти полимерные флокулянты чрезвычайно эффективно образуют мостики между микрохлопьями, возникшими при коагуляции, создавая более крупные макрохлопья.
Затем идет процесс отстаивания. После этого осадок удаляется.
На второй стадии в воду снова добавляются коагулянт и флокулянт, а также вливается осадок, образовавшийся после первой стадии, на крупных частицах которого осаждаются образовавшиеся хлопья осадка. Это способствует более быстрому образованию осадка. Затем идет процесс флотации. Вода аэрируется пузырями воздуха, подаваемого под давлением. При этом пузырьки воздуха слипаются с гидрофобными загрязнениями и всплывают в виде флотокомплексов «хлопья осадка – пузырьки воздуха». Преимущество флотации перед отстаиванием заключается еще и в том, что осадок всплывает к поверхности воды и быстрее происходит его уплотнение. Для доочистки от остаточных загрязнений, находящихся в тонкодисперсном или растворенном состоянии, вода фильтруется.
Образующийся жидкий осадок подвергается обезвоживанию для уменьшения объема. Фильтрат, образующийся в процессе обезвоживания, собирается в резервуаре фильтрата и подается насосом на вторую стадию очистки.
Таким образом, полученные результаты показали высокую эффективность очистки сточных вод лакокрасочного производства методом реагентной флотации с возможностью использования оборотной системы водопользования.
Литература
- Ксенофонтов Б.С. Флотационная обработка воды, отходов и почвы. М., 2010.
- Ксенофонтов Б.С. Проблемы очистки сточных вод промышленных предприятий // Безопасность жизнедеятельности: Приложение к журналу. 2011. № 3.
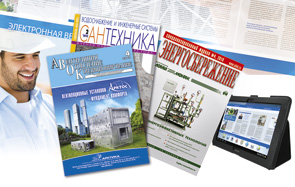
Статья опубликована в журнале “Сантехника” за №6'2012
Статьи по теме
- Москва - город рационального водопользования
Энергосбережение №4'2001 - Водосбережение – рациональное водопользование современных городов
Сантехника №4'2024
Подписка на журналы
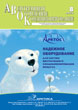
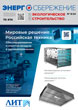
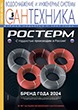