Энергосбережение за счет наладки производственного оборудования на основе энергосервиса
В России механизм энергосервисного контракта (ЭСК) пока только отрабатывается, поэтому интересен любой опыт их внедрения. Приведем один из примеров наладки производственного оборудования, принадлежащего предприятию коммунального хозяйства в г. Дубна, выполненной на условиях ЭСК.
Энергосбережение за счет наладки производственного оборудования на основе энергосервиса
В России механизм энергосервисного контракта (ЭСК) пока только отрабатывается, поэтому интересен любой опыт их внедрения. Приведем один из примеров наладки производственного оборудования, принадлежащего предприятию коммунального хозяйства в г. Дубна, выполненной на условиях ЭСК.
В ходе обязательного энергетического обследования производственных объектов многоотраслевого предприятия коммунального хозяйства наукограда Дубна ОАО «ПТО ГХ»1 была проведена выборочная вибродиагностика 32 агрегатов: 26 насосов, 3 дымососов и 3 вентиляторов, которая выявила 12 агрегатов, остро нуждающихся в центровке. Нами был апробирован и предложен механизм виброналадки оборудования на условиях энергосервисного контракта.
Обследование оборудования
Виброобследование насосных и тягодутьевых машин ОАО «ПТО ГХ» вызвано необходимостью оценки их фактического состояния, проводилось на предприятии впервые для принятия решения о замене дефектных элементов и экономии электроэнергии за счет процедуры лазерной центровки валов: согласования движения двух или более валов друг с другом, которое необходимо выполнять перед их размещением внутри механизма до начала работы оборудования.
Необходимость выверки соосности валов
В настоящее время важность выверки соосности признается всеми специалистами, но на многих предприятиях нет должного отношения к качеству работ по центровке, особенно основного насосного и тягодутьевого оборудования. Однако согласно государственным законодательным документам по энергосбережению2, подход к решению данных вопросов должен стать иным.
Плохая центровка валов является частой причиной повышенной вибрации агрегатов и сопровождается повышенным расходом потребляемой энергии и частыми повреждениями подшипников и соединительных муфт. Использование эластичных муфт при плохой центровке валов снижает вероятность повреждения самих муфт, но не избавляет подшипники от основной причины их преждевременного выхода из строя – от перегрузки вследствие несоосности валов агрегата. Следствием являются повышенные эксплуатационные расходы и снижение производительности оборудования, а в итоге происходит общее снижение прибыльности предприятия.
Если обратиться к статистике, то становится ясно, что причиной преждевременного износа оборудования в 50?% случаев будет именно несоосность. Для сравнения: дисбаланс будет причиной в 40 % случаев.
Анализ вибрации оборудования
Сегодня в большинстве отраслей промышленности используют вибрационный анализ в качестве метода программы предупредительного обслуживания. Анализ вибрации оборудования дает возможность просто обнаружить проблемы, связанные с несоосностью.
Программа виброобследования насосных и тягодутьевых машин ОАО «ПТО ГХ» была разработана на основе шестилетнего практического опыта, полученного на ОАО «Чепецкий механический завод». В базе данных программы есть информация по нормам, предназначенным для оценки состояния вращающихся агрегатов практически всех типов. Программа учитыва-ет состояние агрегата, тип фундамента и соединительной муфты. Технологические параметры, характеризующие работу оборудования (производительность, температура, давление и т. д.), также могут вводиться в программу для проведения анализа их влияния на уровень вибрации агрегата.
Для обработки данных использовалось программное обеспечение «Аврора 2000»3– это сочетание базы данных по оборудованию с экспертной диагностической системой.
Оценка текущего состояния агрегата производится на основании сравнения замеренных значений вибрации с нормированными значениями (ГОСТ ИСО 10816/1–1997 «Вибрация. Контроль состояния машин по результатам измерения вибрации на невращающихся частях. Общие требования»).
Оценка текущего состояния оборудования
Основой для определения текущего состояния оборудования являются измерения среднеквадратичного значения (СКЗ) виброскорости (мм/с), они проводятся на каждом подшипнике оборудования с горизонтальной осью вращения с последовательной фиксацией оси вибродатчика и измерением вибрации в трех взаимно перпендикулярных направлениях: вертикальном, поперечном и осевом (рис. 1), при этом существуют эмпирические правила анализа вибрации:
- горизонтальная вибрация означает дебаланс (Н);
- вертикальная – ослабление или износ фундаментных связей (V);
- осевая – несоосность (А).
![]() |
Рисунок 1. Точки измерения вибрации на подшипниковых опорах насосного агрегата |
Состояние подшипников, качество центровки механизмов, наличие небалансов роторов, правильность монтажа ременных передач и т. д. определяются программой «Аврора 2000».
На основании нескольких замеров вибрации программа определяет время, когда состояние оборудования ухудшается до критического. По итогам проведенных замеров вибрации всего контролируемого оборудования программа оперативно и автоматически формирует график проведения ремонтных работ с указанием дефектов, которые необходимо устранить.
Ярким примером пагубного воздействия чрезмерной нагрузки на подшипники качения, установленные на сетевом насосе марки ЦН 400/105 (№ 3) всего лишь месяц назад, является выход из строя одного из них (рис. 2) по причине ненадлежащего выполнения процедуры центровки.
![]() |
Рисунок 2. Сетевой насос марки ЦН 400/105 (№ 3) |
Раскалывание внешнего кольца подшипника качения данного сетевого насоса могло быть вызвано только двумя причинами: перекосом при монтаже или при больших динамических нагрузках в результате некачественной центровки валов на стадии монтажа агрегата. Учитывая, что относительно недавно перед этим был заменен подшипник качения задней части электродвигателя (рис. 3, точка 1), то можно с большой вероятностью говорить о работе агрегата без должной центровки, которая и спровоцировала ускоренное разрушение подшипников.
![]() |
Рисунок 3. Упрощенная кинематическая схема расположения подшипниковых узлов сетевого насоса марки ЦН 400/105 (№ 3) |
В результате несоосности валов механические и электрические части двигателя испытывают повышенную нагрузку: изнашиваются подшипники (это может стать причиной биения), увеличиваются токи (что приводит к увеличению электрических потерь, более быстрому старению изоляции обмоток), КПД машины резко падает. Работа двигателя в тяжелых режимах ведет к резкому снижению срока эксплуатации, а следовательно, к более частым ремонтам и увеличению затрат на обслуживание данного оборудования.
Виброналадка агрегата
После замены подшипника проведена виброналадка агрегата, которая заключается в выполнении процедуры центровки валов насоса в двух плоскостях (рис. 4). Использование лазерной техники может значительно сократить время центровки, т. к. лазеры обладают высокой точностью и простотой применения. Для этих целей была задействована шведская система центровки валов Easy-Laser D5054, после чего проведены измерения СКЗ виброскорости и оценки огибающей виброускорения измерительным комплексом SKF «CMAS 100 SL».
![]() |
Рисунок 4. Центровка валов насоса в двух плоскостях |
Энергосервисный контракт
Предприятие ОАО «ПТО ГХ» (далее – заказчик), работающее в системе тарифного регулирования, из-за ограниченности финансирования не имеет возможности проводить не запланированные в тарифе работы. Поэтому наша организация (далее – исполнитель) приняла решение провести высокоточную лазерную центровку агрегатов на регулярной основе, на условиях энергосервисного контракта, по которому заказчик, не расходуя собственных средств, проводит улучшение своего энергохозяйства и получает отцентрованные агрегаты.
Исполнитель за свой счет провел процедуру виброналадки оборудования, и под контролем представителя заказчика ежемесячно производит расчет экономии электроэнергии. При этом заказчик в результате эксплуатации оборудования оплачивает услуги (работы) исполнителя за счет средств, полученных от экономии электроэнергии.
По окончании срока энергосервисного контракта заказчик получает все произведенные улучшения оборудования и, естественно, продолжает получать дальше все сэкономленные средства.
Полученная экономия
Приведем пример расчета экономии электроэнергии, достигаемой в результате лазерной центровки сетевого насоса марки ЦН 400/105 (№ 3), установленного в одной из котельных ОАО «ПТО ГХ». Общий алгоритм расчета экономии:
1. Измерить ток до и после проведения центровки.
2. Определить разницу измеренных значений тока.
3. Уточнить характеристики двигателя: напряжение, коэффициент мощности.
4. Выяснить стоимость энергии для предприятия.
5. Рассчитать мощность в кВт по формуле:
W = (V • A • cos (φ) • 1,732)/1 000,
где V – напряжение сети, В;
А – сила тока, А;
cos (φ) – коэффициент мощности.
Годовая экономия составит
Э = Т • ΔW • Ц,
где Т – время работы насоса с учетом фактической загрузки насоса, ч/год;
Δ W – разность мощностей до и после проведения центровки, кВт;
Ц – стоимость покупаемой электроэнергии, руб./кВт ч.
В нашем случае исходные данные для расчета ЭСК следующие:
- мощность электродвигателя сетевого насоса А3 315 М-4У3 Л13 –190 кВт;
- напряжение сети – 380 В;
- время работы насоса с учетом фактической загрузки (при коэффициенте спроса, равном 0,6) – 3 124,8 ч/год;
- тариф покупаемой электроэнергии – 3,2459 руб./кВт•ч;
- cos (φ) – 0,90;
- потребляемый ток, измеренный до центровки,?– 54 А, после центровки – 49 А; соответственно, разница – 5 А.
Рассчитаем мощность до и после проведения центровки:
До: (380 • 54 • 0,9 • 1,732)/1 000 = 31,99 кВт
После: (380 • 49 • 0,9 • 1,732)/1 000 = 29,02 кВт
Экономия в год будет равна: 3124,8 • (31,99 – 29,02) • 3,2459 = 30,12 тыс. руб.
С учетом того, что стоимость полной диагностики сетевого насоса марки ЦН 400/105 (№ 3), включая лазерную центровку, равна 15 тыс. руб., срок окупаемости данного мероприятия составит 6 мес.
По экспертным оценкам, годовой совокупный потенциал экономии электрической энергии в результате процедуры лазерной центровки насосного и тягодутьевого оборудования ОАО «ПТО ГХ» может составить от 450 до 900 тыс. кВт•ч (4–9 % от общего потребления), что в денежном выражении при тарифе на электроэнергию 3,2459 руб./кВт•ч составит от 1,5 до 3,0 млн руб.
Итак, правильная центровка механизмов может снизить потребление энергии электродвигателем в среднем до 10 %, а в некоторых случаях и намного больше.
Никого не удивляют напоминания о выключении света в помещении, если в нем нет необходимости, но кто-нибудь интересовался, сколько электроэнергии можно сэкономить в результате грамотного подхода к виброналадке насоса? А ведь на предприятии средних размеров их может быть несколько сотен. Плохая центровка приводит к потере по крайней мере 3 % стоимости всей производственной энергии.
1 На производственных объектах ОАО «ПТО ГХ» установлено 82 единицы насосного оборудования мощностью от 1,1 до 200,0 кВт, при этом велика доля энергоемких сетевых и канализационных насосов с приводами большой мощности (более 75 кВт) – 39 %. Кроме насосного оборудования, в котельной № 1 установлено 10 тягодутьевых механизмов (5 дымососов и 5 дутьевых вентиляторов).
2 Федеральный закон от 23 ноября 2009 года № 261-ФЗ «Об энергосбережении и о повышении энергетической эффективности и о внесении изменений в отдельные законодательные акты Российской Федерации» и Распоряжение Правительства РФ от 13 ноября 2009 года № 1715-р «Энергетическая стратегия России на период до 2030 года».
3 «Аврора-2000» – экспертная система диагностики состояния и планирования ремонтов вращающегося оборудования по техническому состоянию (Пермь).
4 Сертификат Госстандарта РФ. Система центровки и измерения взаимного расположения поверхностей и вибрации Easy-Laser зарегистрирована в Государственном реестре средств измерений № 31164-06.
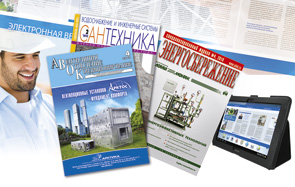
Статья опубликована в журнале “Энергосбережение” за №4'2013
Подписка на журналы
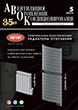
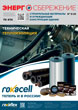
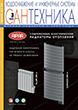