Перевод станционных паровых котлов в конденсационный режим
Conversion of Stationary Steam Boilers to Condensate Mode. Fuel economy method
E.G. Shadek, Candidate of Engineering, Independent Expert, Moscow
Keywords: deep recuperation, combustion products, condensation economizer, heat pump plant, heat economy
The article is a follow-up of article “Assessment of the efficiency of deep utilization of heat from combustion products of power plant boilers” (refer to “Energy Conservation” magazine No. 2, 2016). It offers further development of the technology of deep utilization of combustion products of stationary boilers and gives a specific diagram and operation of the deep utilization unit. It also includes a calculation of the efficiency of the system for boiler plant in the process scheme of CHP .
Статья является продолжением публикации [1]. В ней предложена дальнейшая разработка технологии глубокой утилизации теплоты продуктов сгорания станционных котлов и конкретировано схемное решение и работа узла глубокой утилизации. Также выполнен расчет эффективности системы для котельной установки в технологической схеме ТЭЦ.
Перевод станционных паровых котлов в конденсационный режим
Способ экономии топлива
Статья является продолжением публикации [1]. В ней предложена дальнейшая разработка технологии глубокой утилизации теплоты продуктов сгорания станционных котлов и конкретировано схемное решение и работа узла глубокой утилизации. Также выполнен расчет эффективности системы для котельной установки в технологической схеме ТЭЦ.
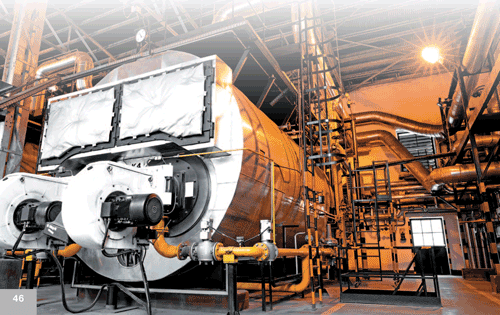
Состояние проблемы
В передовых западных странах глубокая утилизация теплоты продуктов сгорания осуществляется применением водогрейных котлов конденсационного типа, оборудованных конденсационным экономайзером (КЭ) без искусственного хладоносителя, т. е. без применения теплонасосной установки [2, 3].
Отопительные конденсационные котлы получили на Западе массовое применение. За рубежом разрабатываются технологии глубокой утилизации и для паровых котлов [4]. В США начато освоение и выпуск поверхностных конденсационных экономайзеров для паровых котлов. В котельной фирмы «Тимкен» (информация из Интернета) испытан поверхностный экономайзер, установленный за котлом паропроизводительностью 20 т/ч. Температура газов на входе в экономайзер 200 °C, на выходе – 45 °C. Вода в нем (22 т/ч) нагревается с 17 до 46 °C. Теплопроизводительность – более 1,1 Гкал/ч, срок окупаемости – 1,5 года.
В типичной для паротурбинных электростанций технологической схеме конденсат подогревают в газовом подогревателе (ГПК), размещенном в хвостовых поверхностях котла. В нем продукты сгорания охлаждают до температуры не ниже 60 °C во избежание конденсации [5].
После конденсатора насосами (иногда через блочную обессоливающую установку – БОУ) конденсат направляется в газовый подогреватель, после которого поступает в деаэратор. При нормативном качестве конденсата БОУ байпасируют. Для того чтобы исключить конденсацию на последних трубах газового подогревателя, температуру конденсата перед ним поддерживают не ниже 60 °C посредством рециркуляции на вход в него подогретого конденсата. С целью дополнительного снижения температуры уходящих газов в линию рециркуляции конденсата нередко включают водоводяной теплообменник, охлаждаемый подпиточной водой теплосети.
Общие положения. Расчетные данные |
Надежная конденсация водяных паров продуктов сгорания требует их охлаждения до температуры ниже точки росы ТР (для продуктов сгорания природного газа ТР = 50–55 °С), примерно до ТГУ = 40±5 °С. При этом конденсируются пары, содержащиеся в дутьевом воздухе и образующиеся при сжигании углеводородов топлива (метан, водород и пр.). КПД котла в конденсационном режиме1 ηK =105 % (по QРН) [2]. Очевидно, по сравнению с паспортным режимом газового котла с КПД2 92–94 % выигрыш в КПД, а следовательно, экономия топлива, при глубокой утилизации составит 11–13 % от тепловой мощности котла QК. При КПД котла ηK = 100 % удельный расход условного топлива qУД по определению равен 1 ×106 ккал / 7 000 (ккал/кг) = 142,86 кг у. т./Гкал, а при ηK = 105 %, пересчетом 136,06 кг у. т./Гкал. Таким образом можно подсчитать указанные величины для любого случая. С целью получения простых и достаточно надежных соотношений для расчета процесса глубокой утилизации3 обработан большой массив данных для 13 котлов различных марок в диапазоне QК от 8 до 58 МВт и ТУХ от 98 до 194 °С [1]. Коэффициент теплопередачи «продукты сгорания – конденсат» в конденсационном теплообменнике определялся по эмпирической методике завода – изготовителя теплообменника (ОАО «Калориферный завод», Кострома). Получены следующие значения:
Как видно, при глубокой утилизации в 1,22–1,52 раза больше утилизируется теплоты, чем при обычной (сухой). Потенциал сухой утилизации – от 8,0 до 10,6 %, а глубокой – от 10,8 до 14,3 % теплоты от мощности котла QК. Существенный разброс результатов связан в основном с неопределенностью значений температуры ТУХ, меняющейся резко и непрерывно. При всем при этом полученные соотношения позволяют оценить возможности, потенциал и качественно-конкретные показатели исследуемого процесса. Так, по литературным данным 55–60 % теплосодержания продуктов сгорания природного газа составляет теплота парообразования (конденсации), остальное – физическая теплота. Этой пропорции, 60/40, соответствует соотношение QГУТ / q2 = 1,47, что хорошо вписывается в полученный диапазон. Как надежные расчетные характеристики можно принимать величины количества сэкономленной в результате глубокой утилизации теплоты – 10–12 % от мощности котла и удельный расход условного топлива порядка 136 кг у. т./Гкал. |
Решение проблемы
Конденсат паротурбинной установки с температурой 20–35 °C позволяет охладить продукты сгорания в поверхностном газоводяном конденсационном теплообменнике до требуемых 40 °C и обеспечить глубокую утилизацию теплоты.
В основе конструктивного решения (рис.) лежит известная схема: последняя по ходу дымовых газов секция хвостовых поверхностей является водяным конденсационным теплообменником-экономайзером (КЭ) 8. Отличие в том, что КЭ работает в конденсационном режиме, т. е. продукты сгорания охлаждаются не до температуры около 60 °C, а до ТГУ = 40 ±5 °C (см. Общие положения. Расчетные данные).
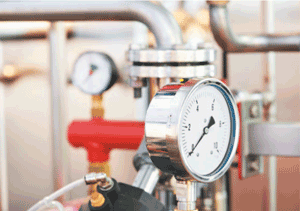
Температура продуктов сгорания сразу за конденсационным экономайзером равна 40 ±5 °C, а после байпаса – 70–90 °C. Поэтому ограждения газохода с узлом глубокой утилизации не требуют огнеупорной футеровки и выполняются из листовой нержавеющей стали с покрытием теплошумоизоляцией. Возможен другой вариант4 схемы – установка конденсационного теплообменника-утилизатора в газоходе сразу за котлом. Узел содержит ту же систему сбора, удаления и очистки конденсата продуктов сгорания.
Конденсационный экономайзер включен в конденсатную линию станции. Этот вариант в статье не рассматривается.
1 Теплотворная способность топлива. Коэффициент полезного действия котлоагрегата |
«Различают низшую и высшую рабочую теплоту сгорания (теплотворную способность) топлива. Низшая рабочая теплота сгорания QНР меньше высшей QВР на то количество теплоты, которая затрачивается на испарение воды, образующейся при сгорании топлив, а также влаги, содержащейся в нем. Высшей называют теплоту сгорания, определяемую без учета затрат теплоты на испарение влаги топлива и влаги, полученной при сгорании свободного и связанного водорода (водород и углеводороды). Например, низшая объемная теплота сгорания природного газа – 31–38 МДж/м3 или 7 400–9 000 ккал/м3. Низшей называют теплоту сгорания, определяемую с учетом затрат теплоты на испарение влаги». [М. С. Ильюхин, Ф. Т. Сидоренков. Основы теплотехники. М. : Агропромиздат, 1987. С. 114.] Величина QPH получается из высшей теплоты сгорания тепла за вычетом тепла, израсходованного на испарение влаги, как имеющейся в топливе – WP, %, так и образующейся при сжигании топлива 9НР, % (около 600 ккал на 1 кг влаги): QPH = QВH – 600(9 • НР / 100 + WP / 100), ккал/кг. В нашей стране (в отличие от США и Великобритании) в теплотехнических расчетах используют низшую теплоту сгорания QPH, при определении которой учитываются затраты теплоты на испарение образующейся при сгорании топлива (углеводородов) воды, поскольку вода обычно выбрасывается с продуктами сгорания в виде пара (несконденсированного). В справочной литературе приводятся, как правило, только значения QPH. Коэффициент полезного действия (КПД) котла (как любой теплоиспользующей установки) ηK равен отношению полезного тепла QПОЛ к израсходованному, т. е. к мощности (теплопроизводительности) котла QK. Тепловая мощность котла QK = В × QPH, где В – расход топлива. QПОЛ, в свою очередь, – разность между QK и суммой тепловых потерь котла ∑q. В эту сумму входят потери: q2 – c уходящими газами, q3 и q4 – вследствие химической и механической неполноты горения соответственно, q5 – рассеянием в окружающую среду (через ограждения): ηK = (QK – ∑q) / QK. (1) Преобладающей является потеря q2. Ввиду малости остальных статей в практических расчетах ими пренебрегают, что близко к реальности, учитывают только величину q2. Тогда формула (1) получает вид: ηK = (em>QK – q2) / em>QK. (2) При глубокой утилизации продукты сгорания ПС, уходящие из котла, охлаждают до температуры ниже точки росы ТР (для ПС природного газа ТР = 50–55 °С), при этом конденсируются водяные пары, как образовавшиеся при сжигании топлива, так и содержащиеся в дутьевом воздухе, а выделившееся тепло испарения (скрытое тепло парообразования) утилизируется и полезно используется (обычно для подогрева обратной воды). В этом случае количество утилизируемого тепла QУТ – это полезное тепло, используемое в технологической схеме котла или котельной. Для подсчета КПД котла ηK.КОНД с глубокой утилизацией (конденсационные котлы) в числителе формулы надо прибавить величину QУТ к полезному теплу котла. В результате получаются значения ηK.КОНД больше 100 %. Очевидно, никакого нарушения закона сохранения энергии здесь нет, а есть принятая в расчетах величина QPH, которая меньше высшей теплотворности QPВ на количество тепла, затраченного на испарение образующейся воды. Рассмотрим тепловые балансы котла в обычном и конденсационном режимах и определение КПД котла по низшей QPH и высшей QPВ теплоте сгорания. С учетом тепла утилизации получим КПД котла в конденсационном режиме ηK.КОНД при расчете по QPH: ηK.КОНД = (QPH – q2 + QУТ) / QPH. (3) В балансе котла для простоты учитывается только статья q2. Так как величина QУТ больше q2, от прибавления в числителе величины QУТ значение ηK.КОНД получается больше единицы. Здесь разность em>QPH – q2 – полезное тепло (от сжигания топлива), реализуемое непосредственно в котле. QУТ – дополнительное тепло глубокой утилизации тепла отработавших в котле продуктов сгорания, привнесенное в технологическую схему котла (котельной). При расчете по QPВ в знаменателе дроби (3) подставляют не QPH, а QPВ, так как для всей технологической схемы котлоагрегата учитывается использование тепла конденсации ПС, входящее в величину QУТ. Этому условию соответствует значение QPВ: ηK.КОНД = (QPH – q2 + QУТ) / QPВ. (4) Верхние индексы Н или В при величинах Q и ηK.КОНД означают, что эти величины относятся (рассчитаны) соответственно к нижней или высшей теплоте сгорания. Покажем расчет КПД для котла ПТВМ-30М, ориентируясь на типичный эксплуатационный режим (статья Е. Шадек, Б. Маршак, А. Анохин, В. Горшков «Глубокая утилизация тепла отходящих газов теплогенераторов», «Промышленные и отопительные котельные и мини-ТЭЦ», 2014, № 2 (23), с. 38–39, табл. 1, столбец 1). Исходные данные: расход газа ВГ = 3 600 м3/ч, температура продуктов сгорания за котлом ТУХ = 130 °С, коэффициент расхода воздуха 1,25, топливо – природный газ с em>QPH = 8 558, QPВ = 9 496 ккал/м3 [М. Б. Равич. Упрощенная методика теплотехнических расчетов. М. : Изд-во АН СССР, 1958, с. 257, табл. 112]; удельный объем влажных продуктов сгорания V = 13,1 м3/м3; теплоемкость продуктов сгорания С = 0,33 ккал/м3•град. 1. Режим без утилизации Тепловая мощность котла по QPВ QКН = ВГ × QPH = 3 600 × 8 558 = 30,808 Гкал/ч. Объем продуктов сгорания W = ВГ × V = 3 600 × 13,1 = 47 160 м3/ч. q2 = С × W × ТУХ = 0,33 × 47 160 × 130 = 2,023 Гкал/ч. По формуле (3) ηKН = (QКН – q2) / QКН = (30,808 – 2,02) / 30,808 = 0,934. 2. Режим с глубокой утилизацией Принимаем величину QУТ равной 11 % от QКН (по опытным и расчетным данным, см. статью) QУТ = 0,11 × QКН = 0,11 × 30,808 = 3,39 Гкал/ч. КПД конденсационного режима по QPН, формула (3): ηK.КОНД = (30,808 – 2,023 + 3,39) / 30,808 = 1,044. Принимаем постоянство расхода газа, ВГ = 3 600 м3/ч. Тепловая мощность QКВ котла по QPВ. QКВ = 3 600 × 9 496 = 34,18 Гкал/ч. КПД конденсационного режима по QPВ, формула (4): ηK.КОНД = (QКН – q2 + QУТ) / QКВ = (30,808 – 2,023 + 3,39) / 34,18 = 0,941. Значения q2 и QУТ не зависят от методики расчета, они остаются неизменными. Близкие значения ηK.КОНД дает расчет и для постоянной тепловой мощности котла QКВ = 30,808 Гкал/ч. Таким образом, при расчете по высшей теплоте сгорания QРВ получены значения КПД в конденсационном режиме меньше 1. Расчеты КПД при глубокой утилизации можно найти в книге А. А. Кудинова «Энергосбережение в теплогенерирующих установках» (М. : Машиностроение, 2012) и других многочисленных публикациях. |
Описание схемы с узлом глубокой утилизации
В распределительном коллекторе 29 (рис.) конденсат при помощи системы автоматического регулирования станции разделяется на два потока:
- первый подается в узел глубокой утилизации в конденсационный экономайзер 8;
- второй – на подогреватель низкого давления 34, а затем в деаэратор 31.
Запорно-регулирующая арматура 30 оборудована приводом и интегрирована в общую систему автоматического регулирования.
![]() |
Рисунок Система глубокой утилизации теплоты продуктов сгорания котлов электростанций |
Выделяющийся из продуктов сгорания конденсат оседает на трубах КЭ и сливается по наклонному днищу газохода в поддон и резервуар 13. Из бака 16 конденсат подается на участок обработки конденсата (не показан), где производят его очистку по известной технологии: нейтрализация – декарбонизация, дегазация. Очищенный конденсат продуктов сгорания подают в подогреватель низкого давления 34 и далее в деаэратор 31 (либо сразу в деаэратор). Далее поток чистого конденсата поступает в подогреватель высокого давления 33, а из него в котел 1.
Работу конденсационного экономайзера и заданный теплосъем в нем поддерживают регулированием количества подаваемого конденсата и объема проходящих дымовых газов посредством байпасирования через байпас 9. Тепловую нагрузку КЭ определяют как оптимальную (не обязательно максимальную) по технико-экономическим и конструктивным соображениям.
Обычно степень байпасирования в аналогичных условиях составляет 0,20–0,25, а в наших расчетах для исследованных котлов – 0,113–0,300 при заданной температуре за узлом глубокой утилизации, после байпаса ТГУ2 = 70 °C.
Оптимальный режим – работа с байпасом в холодное время года, а летом, если опасности конденсации нет, – без него. Отметим, что в данном случае при надежной конденсации и работе каплеуловителя брызгоунос в газовый тракт невелик, и требования к байпасированию, к его степени, температуре ТГУ2 снижаются. Каплеуловитель 11 (его установка не обязательна) размещен в газоходе, в камере со съемной крышкой для обслуживания узла (очистки, смены фильтров, кассет и пр.).
Возможные типы теплообменников
На приведенной схеме показан теплообменник змеевикового типа. В качестве конденсационного экономайзера применимы различные типы теплообменников: кожухотрубные, прямотрубные, с накатанными ребрами, пластинчатые или эффективная конструкция с новой формой теплообменной поверхности с малым радиусом гиба (регенератор РГ 10, НПЦ «Анод»). Рассматриваются также и другие виды:
- теплообменные блоки-секции на базе биметаллического калорифера марки ВНВ123–412–50 АТЗ (ОАО «Калориферный завод», Кострома).
- разборные теплообменники компании «ГЕА Машимпэкс» или цельносварные (типа GEABloc) пластинчатые теплообменники из нержавеющей стали, отличающиеся высокой эффективностью и компактностью.
Сам теплообменник – конденсационный экономайзер, газоход, камера, частично газовый тракт – выполняется из коррозионно-стойких материалов, покрытий, в частности нержавеющих сталей, пластиков – это общепринятая практика [1, 2]. Технология применима и для котлов, использующих другие виды топлива, например древесные отходы, био-синтез-газ и др. Отметим достоинства древесных отходов:
- возобновляемый источник энергии, выбросы СО2 которого нейтральны5;
- низкая коррозионная агрессивность продуктов сгорания;
- возможность конденсировать влагу продуктов сгорания и утилизировать скрытую теплоту парообразования.
Оценка эффективности глубокой утилизации
При оценке системы глубокой утилизации следует сравнивать ее эффективность с эффективностью традиционной схемы с газовым подогревателем конденсата как ближайшего аналога и конкурента.
Принимаем для расчетного примера следующие исходные данные6: котел с QК = 10 МВт/8,6 Гкал/ч, работающий на природном газе с QРН = 8 000 ккал/м3, ТУХ = 130 °C, ηK2 = 0,92 (см. выше), удельный объем продуктов сгорания v = 13,1 м3/м3 (при α = 1,25), расход газа ВГ = 8,6•106/8 000•0,92 = 1 168 м3/ч, потери теплоты с уходящими продуктами сгорания q2 = C•W•TУХ = 763 кВт, где С – теплоемкость, W – объем, ТУХ – температура ПС за котлом.
Далее, принимая отношение QГУТ/q2 равным 1,4 (см. Общие положения. Расчетные данные), получим для системы глубокой утилизации QГУТ = 763•1,4 = 1 068 кВт. Эту величину следует сравнить с теплосъемом в газовом подогревателе конденсата (ГПК). Если температура конденсата на входе в ГПК по требованиям как минимум 60 °C (см. выше), то температура продуктов сгорания на выходе из него будет не ниже 80 °C. Тогда теплосъем в ГПК составит [0,33 × 13,1 × 1 168 × (130 – 80)] / 860 = 294 кВт.
Это в 3,64 раза (1 068 / 294) меньше, чем при глубокой утилизации. Таким образом, выигрыш в теплоте (1 068 – 294) = 774 кВт, что при коэффициенте использования мощности для станционного котла, равном 0,7, даст экономию 554 500 м3 газа в год, или около 3 млн руб. при цене 5 руб./м3. Выигрыш растет пропорционально величине QГУТ, прямо зависящей от мощности котла.
Реконструкция котла требует капвложений. Повышаются эксплуатационные затраты (обслуживание узла глубокой утилизации, расходные материалы для химводоподготовки). Повышение аэродинамического сопротивления газового тракта (узел глубокой утилизации, байпас, каплеуловитель) частично или полностью компенсируется снижением объема продуктов сгорания за счет уменьшения их выхода благодаря экономии топлива и удалению водяных паров. При работе котла под наддувом проблема снимается, что характерно для ряда типов котлов, режимов их работы.
Другие преимущества глубокой утилизации
Кроме повышения тепловой экономичности, система глубокой утилизации обеспечивает:
- снижение эмиссии оксидов NOX с уменьшением температуры продуктов сгорания и в результате подавления водяными парами (орошения продуктов сгорания капельной влагой), вплоть до достижения экологически чистого процесса;
- выработку избыточной воды за счет конденсации; исключается потребность в подпиточной воде и надобность в рециркуляционной насосной установке (экономия электроэнергии) и др. [1].
Важно также отметить, что работа системы глубокой утилизации, заменяющей газовый подогреватель конденсата, в технологической схеме станции не снижает доли электроэнергии в общей комбинированной выработке тепловой и электрической энергии на ТЭЦ и не отражается на общем КПД станции.
Перевод станционного котла в конденсационный режим требует реконструкции котельного агрегата. Последняя сводится в основном к замене на существующем котле водяного экономайзера на конденсационный, переделке главного газохода на участке узла глубокой утилизации с установкой системы слива, удаления и обработки конденсата продуктов сгорания, а также каплеуловителя.
Конденсационный экономайзер отличается от водяного несколько большей поверхностью теплообмена, материалом труб (коррозионно-стойкий), их оребрением. Как видно, предлагаемая схема позволяет минимизировать объем и стоимость работ по реконструкции.
Реализация пилотного проекта откроет перспективы перевода станционных котлов паротурбинных ЭС в конденсационный режим. Станет возможной реконструкция существующих или создание отечественных энергетических конденсационных котлов, тиражирование и масштабная модернизация котельных. В любом случае в порядке предпроектной проработки для выбранного объекта выполняются ТЗ, ТЭО, рекомендации, экспертиза, выбор решения и пр., и в случае положительных результатов – проектирование и реализация.
Литература
- Шадек Е. Г. Оценка эффективности глубокой утилизации тепла продуктов сгорания котлов электростанций // Энергосбережение. 2016. № 2.
- Шадек Е., Маршак Б., Анохин А., Горшков В. Глубокая утилизация тепла отходящих газов теплогенераторов // Промышленные и отопительные котельные и мини-ТЭЦ. 2014. № 2 (23).
- Шадек Е., Маршак Б., Корыкин И., Анохин А., Горшков В. Конденсационный теплообменник-утилизатор – модернизация котельных установок // Промышленные и отопительные котельные и мини-ТЭЦ. 2014. № 5 (26).
- ООО «Бош Термотехника». Полное использование теплоты сгорания // Промышленные и отопительные котельные и мини-ТЭЦ. 2014. № 5 (26). С. 26–31.
- Березинец П., Ольховский Г. Перспективные технологии и энергоустановки для производства тепловой и электрической энергии. Раздел шестой. 6.2. Газотурбинные и парогазовые установки. 6.2.2. Парогазовые установки. ОАО «ВТИ». «Современные природоохранные технологии в энергетике». Информационный сборник под ред. В. Я. Путилова. М. : Издательский дом МЭИ, 2007.
2 На практике КПД не превышает 90 %.
3 Расчет процесса глубокой утилизации (определение QУТ и др.) проводили по инженерной методике, описанной в [2].
4 Данный вариант в статье не рассматривается.
5 Древесные отходы не считаются в общем балансе выбросов парниковых газов.
6 Подробнее см. справку «Пример простейшего расчета баланса котла» в [1].
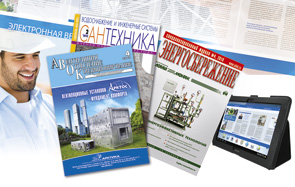
Статья опубликована в журнале “Энергосбережение” за №6'2016

Статьи по теме
- Применение кольцевых теплонасосных систем
АВОК №4'2006 - Геотермальная система теплоснабжения с использованием солнечной энергии и тепловых насосов
Энергосбережение №3'2008 - От централизованного теплоснабжения – к тепловым насосам
Энергосбережение №3'2010 - Тепловые насосы для российских городов
Энергосбережение №1'2011 - Эволюция тепловых насосов
Энергосбережение №5'2011 - Системы отопления на базе теплонасосных установок. Подмосковный опыт
Сантехника №4'2012 - Использование тепловых насосов для подогрева воды в бассейнах
Сантехника №2'2013 - Оценка эффективности глубокой утилизации тепла продуктов сгорания котлов электростанций
Энергосбережение №2'2016 - Применение теплонасосных установок для отопления и горячего водоснабжения жилых домов. Опыт Австрии
АВОК №8'2013
Подписка на журналы

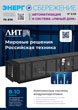
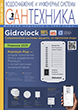