«РИФАР»: качество как философия
От одного литейного комплекса до высокотехнологичного производства современных секционных и трубчатых радиаторов отопления и собственного трубного производства – такой путь проделала компания «Рифар» за 21 год работы. Что стоит за успехом, редакции журнала рассказал Александр Игоревич Солодченко, директор московского представительства АО «РИФАР» – члена НП «АВОК» категории «Премиум».
«РИФАР»: качество как философия
От одного литейного комплекса до высокотехнологичного производства современных секционных и трубчатых радиаторов отопления и собственного трубного производства – такой путь проделала компания «Рифар» за 21 год работы. Что стоит за успехом, редакции журнала рассказал Александр Игоревич Солодченко, директор московского представительства АО «РИФАР» – члена НП «АВОК» категории «Премиум».
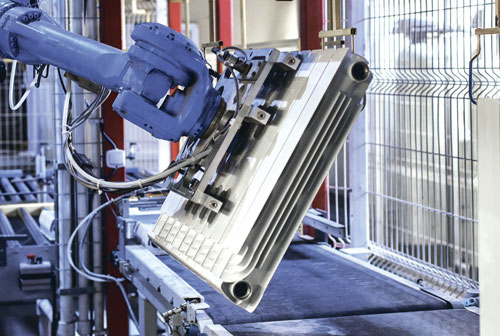
Компания прошла интересный путь, есть чем гордиться. Давайте перечислим основные вехи.
Компания «Рифар» основана в 2002 году, в 2003-м начат выпуск первых биметаллических радиаторов под маркой RIFAR, адаптированных для российских условий. Следом начался период, который коротко можно охарактеризовать как «Мы – первые в мире»: в 2005-м первыми выпустили биметаллические радиаторы изогнутой формы для эркеров; в 2008-м – биметаллические радиаторы с нижним подключением со стандартным подсоединительным размером 50 мм и алюминиевые радиаторы новой конструкции (обжимная нижняя заглушка и новые уплотнения обеспечили давление разрушения не менее 60 атм.); в 2009-м – монолитные биметаллические радиаторы MONOLIT с разрушающим давлением свыше 150 атм. 2010 год отметился цельнолитыми биметаллическими радиаторами с самым низким межосевым расстоянием – 200 мм. В 2012-м установили мировой рекорд производительности литейных комплексов при производстве секционных радиаторов. В 2016 году впервые в мире нами произведен радиатор с использованием множественных плоскостей разъема пресс-форм, что позволило создать принципиально новый дизайн радиаторов SUPReMO. Тогда же была выпущена 50-миллионная секция, а в следующем году построено и запущено собственное производство стальных труб.
В 2018-м мы успешно прошли сертификацию производства и продукции в рамках внедрения новых требований на соответствие ГОСТ 31311-2005. К серийному выпуску алюминиевых радиаторов с нижним подключением с присоединительным размером 50 мм приступили в 2019 году. В 2021-м была произведена 100-миллионная секция биметаллического радиатора, а в прошлом году начато серийное производство вертикальных биметаллических радиаторов RIFAR CONVEX.
За 21 год мы создали эффективное предприятие, отличающееся высокими стандартами и требованиями к продукции.
Почему выбор пал на секционный радиатор?
Если смотреть с точки зрения машиностроения, то секционный радиатор – это изделие, которое с минимальным количеством операций превращается в продукт, полностью готовый к реализации. Да, в производстве радиаторов есть свои сложности и их немало, но это тот формат производства, который позволяет очень быстро получать продукцию. Литье под давлением, используемое в производстве радиаторов, дает возможность получать изделие с минимальной доработкой: отлили, отшлифовали, сформировали резьбы, покрасили – готов радиатор. Именно поэтому были выбраны секционные радиаторы. Тогда, в 2002 году, это было сложное производство, гораздо сложнее, чем изготовление панельных радиаторов или конвекторов. И это важно: выбирая для себя модель производства, бизнеса, надо стремиться делать сложные вещи, тогда ты долгое время будешь находиться вне конкуренции.
Какое оборудование входит в производственный комплекс?
Все начиналось с одной литейной машины. Да, на тот момент еще не было ни внутренних стандартов компании, ни понимания рынка. Это пришло позже, но с самого начала мы не просто ориентировались при производстве радиаторов на ГОСТ 31311, а ставили задачу достижения характеристик, превосходящих нормативные. Были освоены технология литья под давлением и технология подготовки поверхностей, разработаны стандарты компании и введен контроль качества продукции. И сегодня «Рифар» – современное высокотехнологичное производство, включающее 10 автоматизированных литейных комплексов.
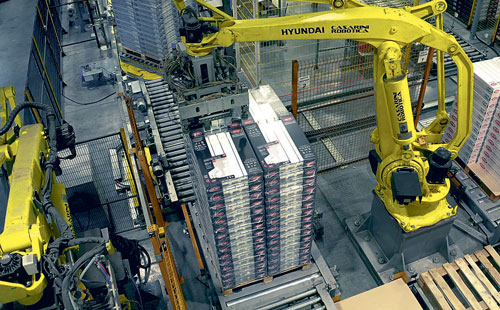
Краеугольный камень производства секционных радиаторов – это литье под давлением. Цех оборудован плавильной газовой печью итальянского производства, в которой происходит плавка и разливка алюминия. Высококачественный алюминиевый сплав российского производства, поддержание постоянной температуры, строгое дозирование объема металла позволяют свести к минимуму затраты на отходы производства.
Но производство – это не только высокотехнологичные линии. Многие производители поверхностно относятся к конструкторской документации, в «Рифаре» другой подход – сначала проектирование, потом производство. Очень много тонкостей кроется в разработке самого изделия. И только когда оно уже сформировано на бумаге и оформлено в конструкторскую документацию, посчитаны тепловая мощность прибора, масса, площадь оребрения, известны размеры закладных элементов, площадь отливки и, соответственно, площадь, которую придется укрывать краской, можно переходить к производству.
Конвейерное производство – это монотонный труд, перемещение достаточно больших грузов (только один 14-секционный радиатор весит 28 кг), сортировка, если идет несколько моделей радиаторов, – все это требует автоматизированных линий. Как и дополнительные операции – шлифовка, последующая обработка, покраска. Поэтому была сделана ставка на максимальную автоматизацию производства, которая полностью себя оправдала, обеспечила высокие показатели качества продукции и позволила систематизировать работу завода. Сейчас производство радиаторов и разгрузка конвейера ведутся промышленными роботами MOTOMAN и ABB.
Литейное производство «Рифар» полностью автоматизировано, как и процессы распознавания качества изделия, покраски и оценки качества покраски, сборки, испытаний, упаковки. Мало того – чтобы все вышеперечисленные процессы работали, изделия должны быть одинаковыми: техническое зрение, которое в т.ч. применяется на «Рифаре», не очень любит вариативность. Радиатор должен банально иметь ровные поверхности, чтобы захваты для загрузки-разгрузки конвейера правильно работали. Для нас серийное массовое производство – не пустые слова. Мы прекрасно знаем, чем отличается просто производство от массового, и риски, которые с этим связаны, нивелируются именно сложностью оборудования, глубокой инженерной проработкой. Мы уделяем этому максимальное количество времени и ресурсов.
Производству предшествует большая предварительная работа. Что она включает?
В первую очередь это работа конструкторского отдела компании, который формирует целый пул задач и одновременно их решения. На сегодняшний день конструкторский отдел – это не просто подразделение, которое рисует какое-то изделие, готовит чертежи, создает документацию. Это отдел, который создает пресс-формы, дополнительный инструмент, новые станки, новые изделия, методики испытаний. И все это воплощается на одном заводе. Кроме того, в зоне ответственности конструкторского отдела управляющие программы. Повторюсь, на сегодняшний день у нас выстроено и работает полноценное инструментальное производство с фрезерной, токарной, электроэрозионной, шлифовальной и измерительной группами, которыми необходимо управлять. При этом основа производства – импортные станки, в работе которых мы разбираемся на уровне их производителей. Мы не работаем с оборудованием, параметров которого не знаем.
Станки импортные, а что по поводу комплектующих?
«Рифар» – компания с высокой степенью локализации. Практически все, что производится и называется радиатором отопления, изготавливается на нашем заводе. На производство поставляется полиэтиленовая пленка и сталь в рулонах, алюминий в слитках, краска. Все комплектующие отвечают внутренним стандартам компании. Например, российская сталь, закупаемая для наших радиаторов, – очень чистая, с особыми антикоррозионными свойствами. Мы производим приборы отопления, которые контактируют с водой, и хотим, чтобы они работали долго и эффективно. Поэтому покупаем холоднокатаную сталь высокого качества, сделанную под заказ для «Рифара». По этому пути в России пока не идет никто, т. к. это дороже. Мы сознательно делаем эти шаги.
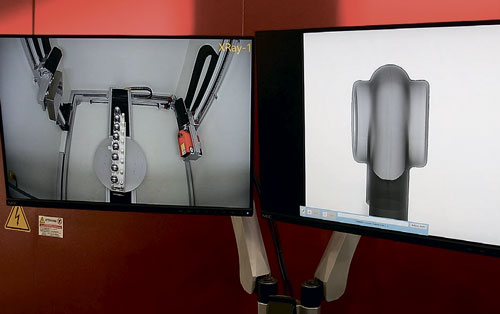
Краска немецкого производства, в качестве которой мы тоже уверены.
Еще одна импортная составляющая нашего производства – уплотнительные кольца, которые не изготавливают в России. Производство уплотнителей – это отдельное высокотехнологичное производство, как правило, ориентированное на гигантов автомобилестроения. Поэтому открывать производство для обеспечения исключительно собственных нужд не имеет смысла.
Если говорить о комплектующих для станков, то и это решаемо, несмотря на то что литейные линии, вспомогательное периферийное оборудование – итальянского производства, а роботы – японские. В современном мире нерешаемых задач практически нет.
Как осуществляется контроль качества?
Надежность нашего оборудования обусловлена совокупностью мер и подходов к производству, которые позволяют производить качественную продукцию.
Мы осуществляем контроль сырья (сталь Correx), труб (химический состав, геометрия, сварной шов), сварного шва, резьб по ГОСТ 6357, герметичности после сборки и после окраски, качества поверхности и адгезии покрытия, а также рентгенографический контроль.
Во многом это ответственность «Рифар лаб» – подразделения, которое объединяет металлографическую и химическую лаборатории. Лаборатория, которая создавалась как банальный химанализ расплава (у некоторых предприятий этого нет до сих пор), сегодня – это оценка и создание методов испытаний, определение механических свойств металлических материалов и синтетических каучуков, оценка качества продукции, создание методик измерения. Работа «Рифар лаб» распространяется и на физический контроль всех материалов, которые мы используем, и на готовую продукцию. Без заключения лаборатории мы не примем в работу ни металл, ни трубу собственного производства. Мы тратим много времени, ресурсов, сил на обучение квалифицированного персонала, способного обес-печить такой подход. Таким образом, мы создали систему качества, удовлетворяющую самых взыскательных клиентов, которые проводят у нас аудиты, приезжают знакомиться с методами контроля.
Компания долго шла к автоматизированным стендам для оценки продукции. Все радиаторы «Рифар» дважды проходят испытания на герметичность. Испытания статическим давлением осуществляются с существенным превышением нормативов ГОСТов. Условно, если обычно радиаторы испытываются на 30–45 атм., то в «Рифаре» нормальной практикой считается 250 атм., есть радиаторы, которые выдерживают более 500 атм. – серии MONOLIT и SUPReMO.
Чем вызван такой подход?
В первую очередь это важно нам как инженерам: проверить не просто качество сварных швов, но и их прочность, надежность. Завод должен выпускать надежную продукцию, за которую не стыдно.
Наши радиаторы смонтированы на различных объектах, эксплуатируются в самых разных условиях – например, в лаборатории по выращиванию семян, а это спецклимат и спецусловия, огромная стоимость семенного фонда. В случае аварийной ситуации никаких страховок не хватит, чтобы возместить ущерб. Радиаторы «Рифар» стоят и в труднодоступных местах, куда невозможно просто вызвать сантехника в случае поломки: на газовых платформах, на судах ледокольного флота.
А если все-таки что-то случилось?
У нас есть две сервисные услуги, которые максимально отвечают потребностям наших клиентов и помогают решить возникшие проблемы.
Первая – это консультации для конечных потребителей. Мы – производители и всегда оставляем возможность любому физическому лицу позвонить в офис компании и задать нам вопрос или рассказать о проблеме.
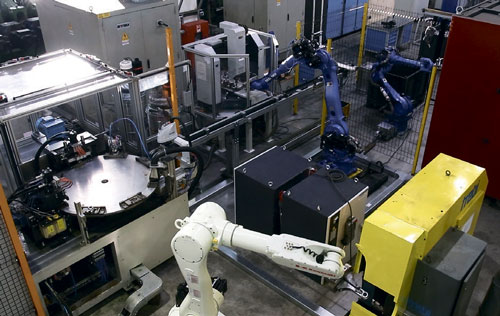
Вторая услуга – мобильная экспертиза. В случае аварии на место выезжает мобильная лаборатория, берутся пробы теплоносителя, выясняются все нюансы эксплуатации, дается заключение и, как правило, осуществляется замена радиатора. Иногда, в случае прямого нарушения условий эксплуатации, можем написать отказ, но в большинстве случаев меняем. Как правило, это зимний период – мы не оставляем людей замерзать. Мы всегда готовы идти навстречу и открыты для диалога. Для нас, как для инженерной компании, важно разобраться в причинах произошедшего. Если причина найдена, у нас появляется задача, которую надо решить, чтобы двигаться дальше и делать продукцию еще качественнее.
Мы ответственно подходим к взаимодействию с конечным потребителем: отдавая прибор, обязательно сопровождаем его паспортом готовой продукции. Это тот документ, посредством которого мы общаемся с потребителем. Когда производитель максимально полно описывает все нюансы эксплуатации продукции – это уважение к клиенту.
Есть ли дополнительные услуги для специалистов?
Наша продукция реализуется через дилерскую сеть, соответственно, мы проводим обучающие семинары для дилеров. Обучающий семинар по одному типу радиаторов длится четыре часа, в которые мы пытаемся вложить наш 20-летний опыт производства. Считать ли это дополнительной услугой? Для нас это неотъемлемая часть работы.
Естественно, есть семинары для проектировщиков и монтажников, которые по определению разные. В зависимости от потребностей слушателей мы ведем, можно сказать, персонализированные семинары.
Перспективы и планы?
Второй год мы развиваем линейку стальных трубчатых радиаторов под торговой маркой TUBOG. В силу того, что многие европейские компании покинули рынок, нагрузка на это производство возросла. И сейчас нам необходимо его немного диверсифицировать и интенсифицировать. Мы направили все наши усилия на развитие производства TUBOG для его полноценной нормальной работы по стандартам «Рифар».
Важно понимать, что ни одно предприятие одновременно не выпускает трубчатые радиаторы и литые секционные. Это сложно. Все разное: клиентские группы, цветовые решения (особенно в трубчатых радиаторах), упаковка, требования, комплектация, огромный типоразмерный ряд. Несмотря на то что мы решили четыре основные проблемы трубчатого радиатора (толщина стенки; покраска; рентгенографический контроль, который пока никто не применяет; изменение схемы нижнего подключения на правильную гидравлическую схему), остались еще вопросы, связанные с цветом. Рынок требует большого разнообразия цветовых решений. Мало того что типоразмерный ряд TUBOG описывается 210 тыс. зарегистрированных штрих-кодов, так умножьте это число еще на 70 цветов! Для того чтобы справиться с такими задачами, нужна система управления, позволяющая клиенту нормально, без надрывов, получить радиатор, который он хочет, в нужное время, нужного цвета, с должными гарантийными обязательствами и отношением завода.
Мы стараемся сделать продукт, который даже лучше, чем то, к чему привык рынок. Этим и будем заниматься в ближайшее время!
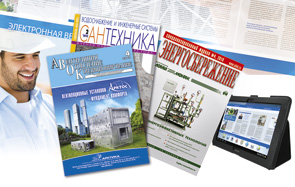
Статья опубликована в журнале “АВОК” за №5'2023

Статьи по теме
- Радиаторы «Теплоприбор»: дизайн, инновации, качество
АВОК №4'2024 - Проблемы межсекционного соединения биметаллических радиаторов отопления
Сантехника №3'2024 - Чек-лист: выбираем биметаллический радиатор отопления
АВОК №5'2024 - Рекорды RIFAR: 100-миллионная секция биметаллического радиатора
Сантехника №6'2021 - Радиатор RIFAR ECOBUILD – задача по геометрии
Сантехника №4'2024 - Производство стальных трубчатых радиаторов TUBOG
Сантехника №5'2022 - РИФАР – 20 лет бескомпромиссного качества
АВОК №1'2023 - Компания «Изотерм» развивает направление дизайна в приборах отопления
АВОК №3'2023 - Проблемы межсекционного соединения биметаллических радиаторов отопления
АВОК №6'2021 - RIFAR BASE – 21 год
Сантехника №4'2023
Подписка на журналы
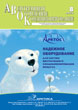
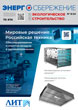
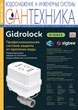